All About Alcast Company
All About Alcast Company
Blog Article
7 Simple Techniques For Alcast Company
Table of ContentsThe Best Strategy To Use For Alcast CompanyAlcast Company for BeginnersHow Alcast Company can Save You Time, Stress, and Money.Alcast Company - The FactsThe Alcast Company DiariesAll about Alcast Company
The subtle difference hinges on the chemical web content. Chemical Comparison of Cast Light weight aluminum Alloys Silicon advertises castability by decreasing the alloy's melting temperature level and boosting fluidness during spreading. It plays a vital duty in enabling complex mold and mildews to be filled precisely. Furthermore, silicon adds to the alloy's stamina and wear resistance, making it important in applications where toughness is vital, such as auto components and engine parts.It additionally enhances the machinability of the alloy, making it easier to refine right into ended up products. By doing this, iron adds to the overall workability of aluminum alloys. Copper raises electric conductivity, making it useful in electric applications. It likewise enhances corrosion resistance and includes in the alloy's total toughness.
Manganese adds to the strength of light weight aluminum alloys and enhances workability. Magnesium is a lightweight component that offers toughness and influence resistance to aluminum alloys.
The smart Trick of Alcast Company That Nobody is Discussing
Zinc boosts the castability of light weight aluminum alloys and assists regulate the solidification process during spreading. It boosts the alloy's strength and hardness.
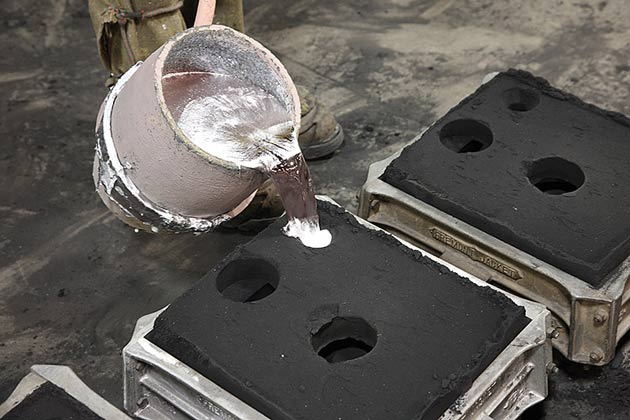
The main thermal conductivity, tensile strength, return toughness, and prolongation differ. Select appropriate resources according to the efficiency of the target product created. Amongst the above alloys, A356 has the highest possible thermal conductivity, and A380 and ADC12 have the least expensive. The tensile limit is the opposite. A360 has the best return strength and the highest elongation price.
How Alcast Company can Save You Time, Stress, and Money.

In accuracy casting, 6063 is fit for applications where intricate geometries and premium surface area finishes are paramount. Instances include telecommunication units, where the alloy's exceptional formability permits smooth and cosmetically pleasing designs while preserving structural stability. In a similar way, in the Illumination Solutions market, precision-cast 6063 elements produce elegant and effective illumination fixtures that need detailed forms and great thermal efficiency.
It brings about a better surface area finish and better corrosion resistance in A360. Furthermore, the A360 shows exceptional elongation, making it ideal for facility and thin-walled elements. In precision casting applications, A360 is fit for sectors such as Customer Electronics, Telecommunication, and Power Tools. Its enhanced fluidity permits intricate, high-precision components like smartphone casings and interaction tool real estates.
Alcast Company for Dummies
Its special buildings make A360 a beneficial option for accuracy casting in these industries, boosting product longevity and high quality. Light weight aluminum alloy 380, or A380, is a widely utilized casting alloy with a number of distinct features. It provides superb castability, making it a perfect selection for precision casting. A380 exhibits good fluidity when molten, ensuring complex and in-depth molds are properly reproduced.
In accuracy casting, light weight aluminum 413 shines in the Consumer Electronic Devices and Power Equipment sectors. This alloy's premium deterioration resistance makes it an exceptional selection for outside applications, guaranteeing lasting, long lasting products in the mentioned markets.
The Buzz on Alcast Company
Once you have decided that the light weight aluminum pass away casting process is ideal for your project, a crucial next step is choosing the most suitable alloy. The light weight aluminum alloy you choose will considerably impact both the spreading process and the homes of the end product. Due to the fact that of this, you should make your choice meticulously and take an enlightened method.
Establishing the most appropriate light weight aluminum alloy for your application will certainly mean weighing a vast range of attributes. These relative alloy attributes follow the North American Die Casting Organization's guidelines, and we've split them into two categories. The initial category addresses alloy qualities that affect the manufacturing process. The second covers characteristics impacting the residential or commercial properties of the end product.
Excitement About Alcast Company
The alloy you select for die casting straight influences a number of aspects of the spreading process, like how very easy the alloy is to collaborate with and if it is prone site link to casting issues. Hot fracturing, additionally called solidification cracking, is a normal die casting problem for light weight aluminum alloys that can result in internal or surface-level rips or splits.
Specific light weight aluminum alloys are more prone to warm cracking than others, and your choice should consider this. It can damage both the cast and the die, so you should look for alloys with high anti-soldering buildings.
Corrosion resistance, which is already a remarkable feature of aluminum, can vary considerably from alloy to alloy and is an essential particular to take into consideration depending on the environmental conditions your item will certainly be subjected to (Aluminum Casting). Wear resistance is another building generally sought in aluminum items and can differentiate some alloys
Report this page